Actuation
Design
To actuate these mechanisms, we have developed lattice-scale actuators that can be assembled just like every other part of our assembly system. We use voice coil actuators for their power density, stroke, and relative ease of fabrication. Each actuator is composed of two parts: a magnetic part and a coil part. The magnetic part is made of a permeable material such as iron or steel and houses two magnets, which are arranged to produce two regions of high flux density. The coil part fits within these regions of high flux density to produce a force when energized with a current. The composition of this actuator is pictured below and includes a coil wrapped around mandrel parts and a magnetic part which concentrates flux into two small regions where the coil slides.
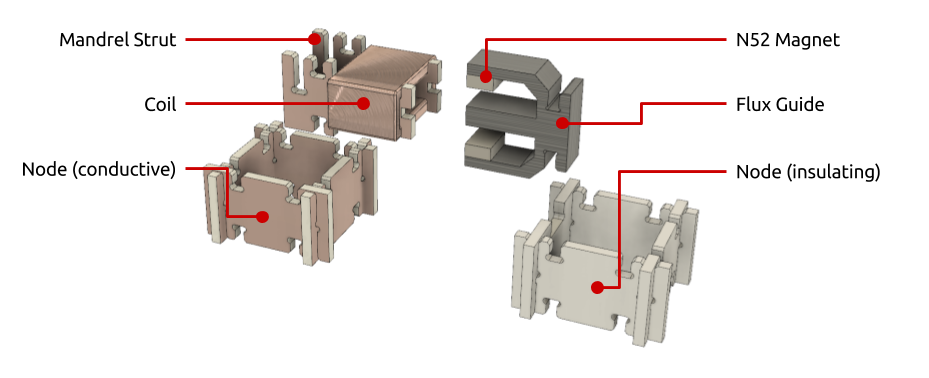
Scaling down the first walking motor prototype first involved improving the actuator performance. If we relax the constraint that the actuator is bounded to the envelope of a single strut, we can make 2x and 4x actuators which take up the volume of two struts and four struts respectively. The added advantage is that we can reclaim the volume occupied by one and two nodes respectively in these arrangements. This leads to a significant improvement in energy density for 1x vs 2x. The improvement is smaller between 2x and 4x because the extra volume that is used in the 4x is not terribly used in the 2x.
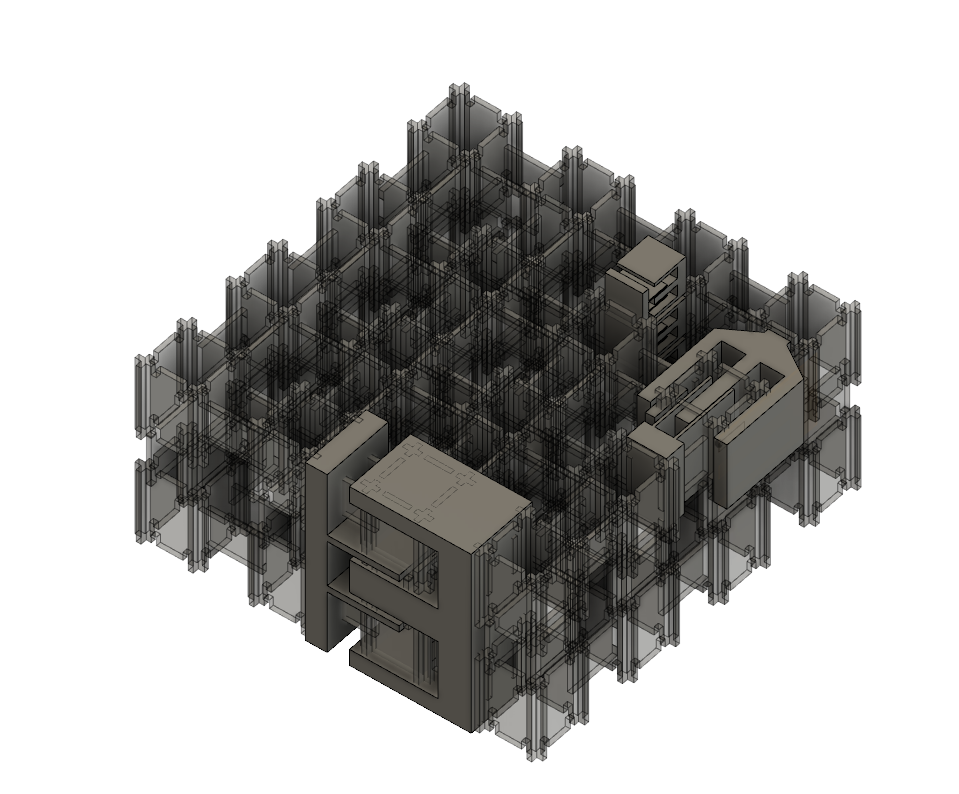
Simulation
I roughly model the voice coil actuators using magnetic circuit theory to calculate the magnetic field across the coil and calculate the the resulting Lorentz force. From this we can see that the initial design is expected to produce about 200mN of force with 1A of current. This assumes magnets that are 3mm x 2mm x 1mm, a coil that is 1mm thick, and with 0.25mm of air-gap left on either side of the coil.
By increasing the magnet size to 6mm x 3mm x 2mm, and the coil-thickness to 2mm, we can increase the expected force to approximately 1N. This requires slightly more complicated geometry to achieve but may be do-able without introducing too many custom or difficult-to-machine parts.
Testing
Qualitative
I test the actuators qualitatively by building them into mechanisms and powering them using an H-Bridge to switch current through the coils bi-directionally.
Quantitative
I measure the force produced by the actuators using my table-top Instron.
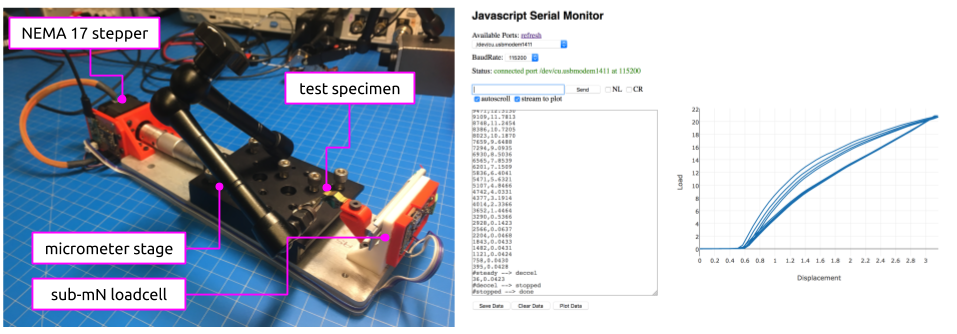
Initial testing indicates that the actuator is only producing approximately 50mN of force with 1A of current (supplied directly from a current-limited power supply). This is corroborated by the fact that it can lift a 5g bolt but fails to lift a 10g mass under these conditions.
While testing the coil at 1.5A, I realized that the coil was becoming hot enough to melt the delrin mandrel parts (but not before destroying the parts). It took less than 30 seconds to reach that temperature which means that 1.5A is a firm upper-limit unless it is used with very short duty-cycles.