Assembling a Millimeter-Scale Walking Motor
Part Fabrication
Parts are fabricated in largely the same way as in the larger scale prototype. Structural node and strut parts are cut on the EDM.
The actuator is composed of two parts: the coil and the magnetic core. Both the coil mandrel and the magnetic core are made on the EDM.
The coil mandrel is then wound with ~34 turns of 34AWG wire. This is sub-optimal winding. With more careful winding, I calculate that I should be able to fit approximately 90 turns. This would increase the performance of the actuator considerably and will likely be possible as I revise the process of producing these actuators.
The magnetic core needs to be taken down from ~2.5mm to 2mm in thickness. This can either be done with rigorous sanding or by machining. The magnets are then inserted into the core. For this prototype, there are no off-the-shelf magnets which fit the required dimensions (2.8mm x 2mm x 0.5mm), so instead, I assemble three 2mm x 1mm x 0.5mm magnets to form the desired shape. This requires gluing each magnet in place one-by-one since they repel each other.
The 2-DOF flexural parts are made using the composite laminate layup technique. This involves individually machining five layers using the Oxford laser and then heating and squishing to form the final laminate. I use 2 layers of 0.004" brass for the rigid material and a 0.001" kapton layer for the flexible hinges. These layers are joined by two layers of 0.0005" pyralux adhesive.
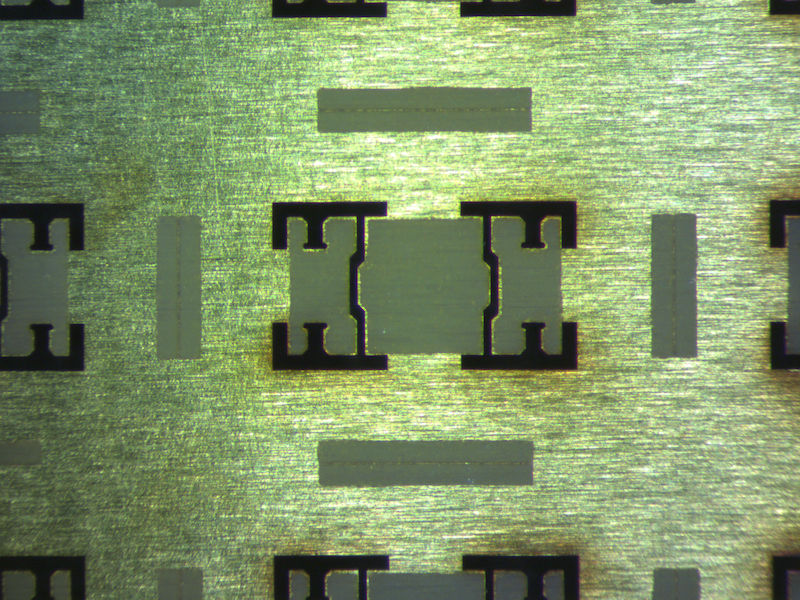
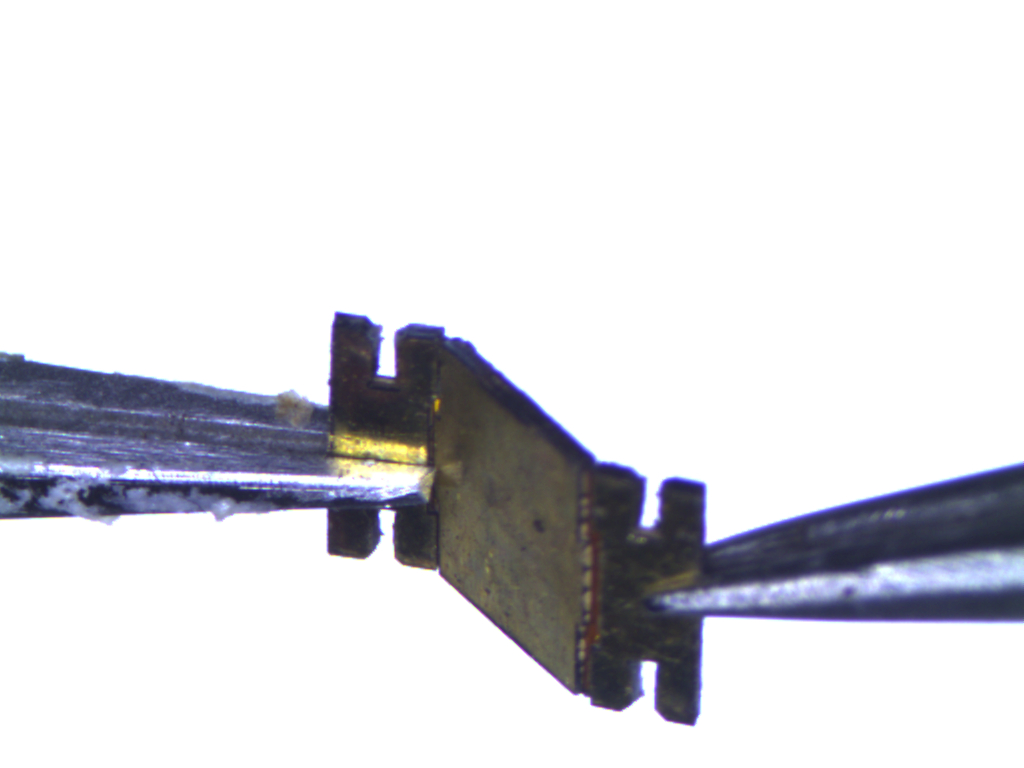
Assembly
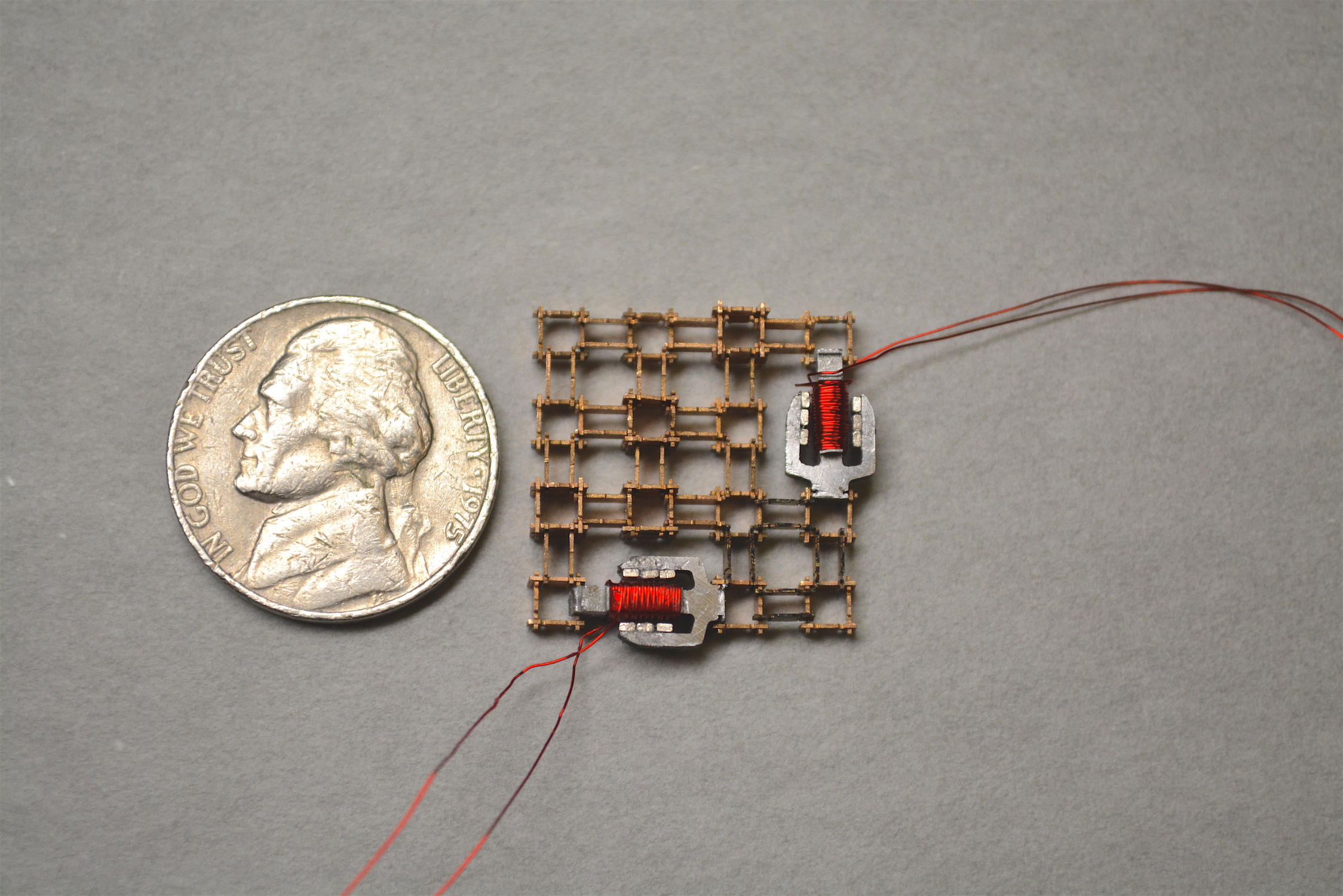
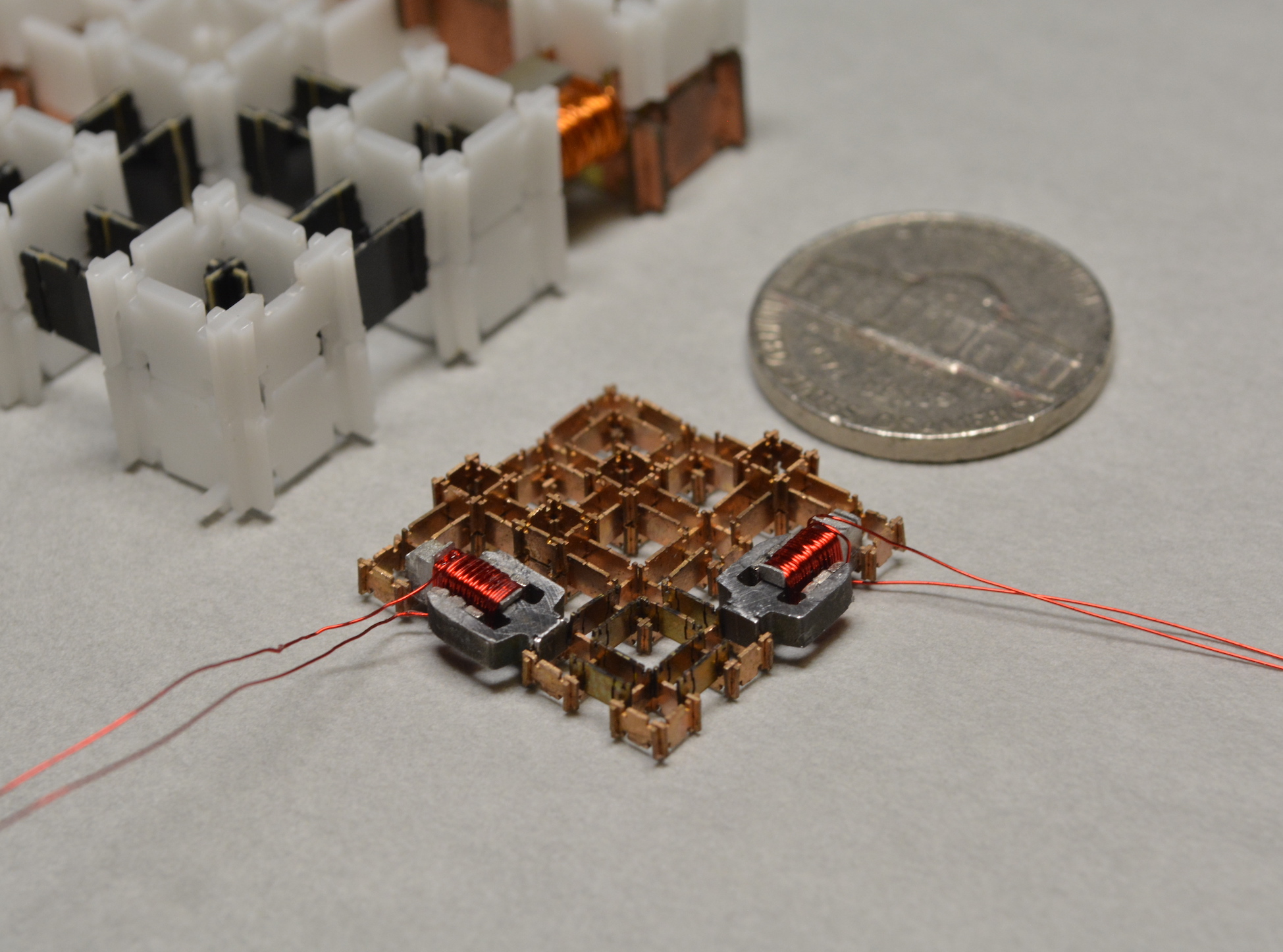